Service & Support
We are committed to providing professional technical support, prompt after-sales service, and reliable logistics assistance to our global partners.
Rubber Expansion Joint Installation Manual
Frequently Asked Questions
Typically 5–10 years depending on the application environment, material type, and installation quality. Proper maintenance can extend its service life.
Yes, we offer customization for flange standards (DIN, ANSI, JIS, etc.), pressure ratings, and joint lengths.
Our rubber joints are manufactured under ISO 9001 standards and can provide CE, WRAS, and third-party inspection certificates upon request.
Store in a cool, dry, and shaded environment. Avoid direct sunlight, ozone, or contact with petroleum-based liquids.
Yes, we provide detailed manuals and remote guidance via WhatsApp or Email for international customers.
Logistics & Shipping Information
Company Gallery
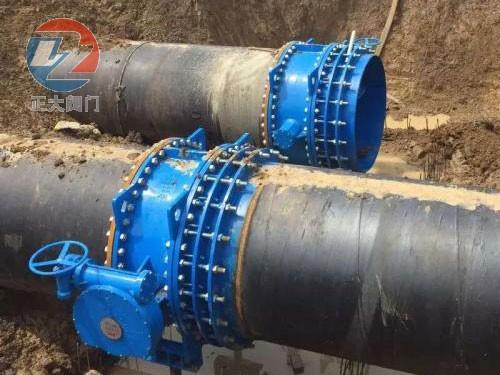
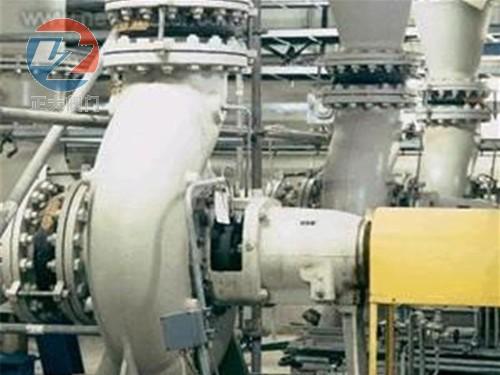
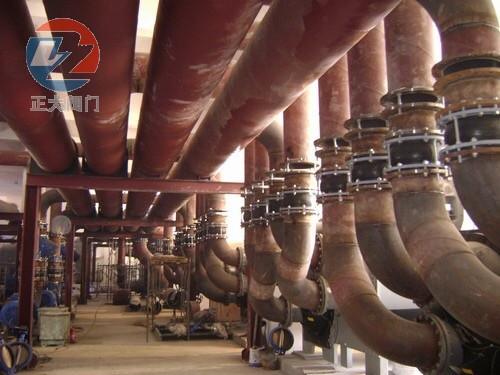

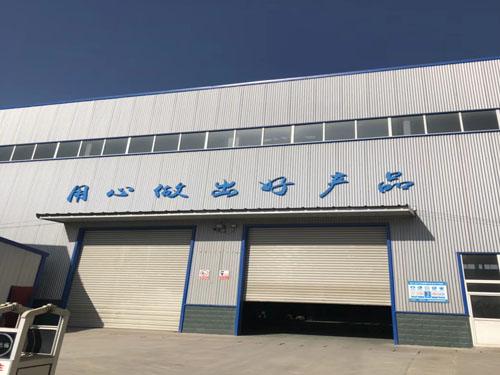
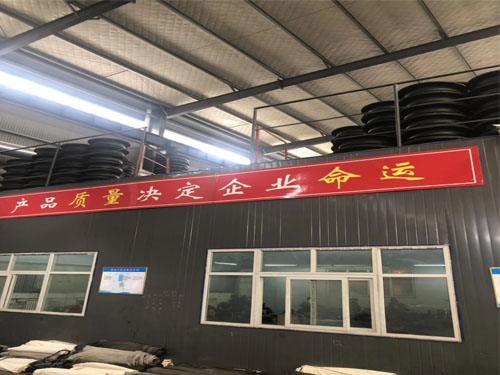
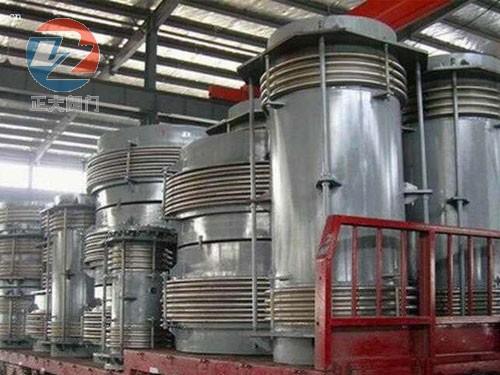
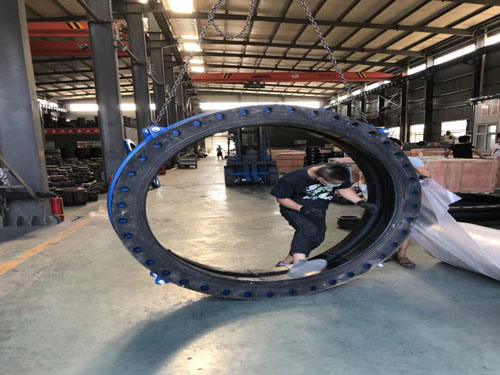
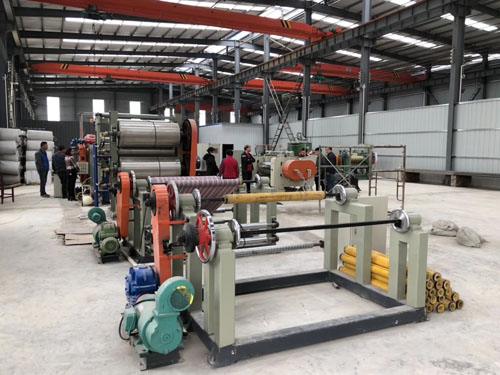
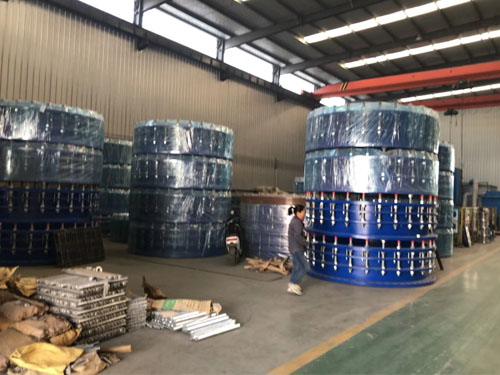
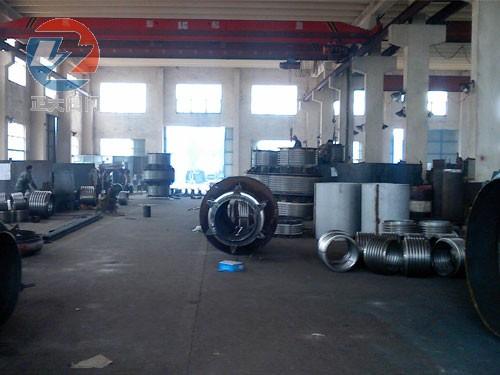
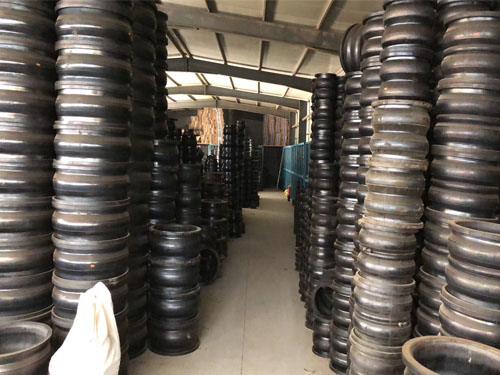
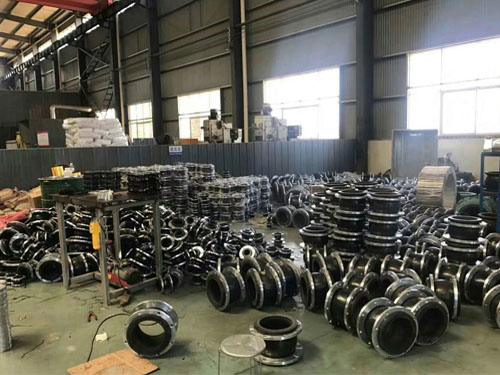
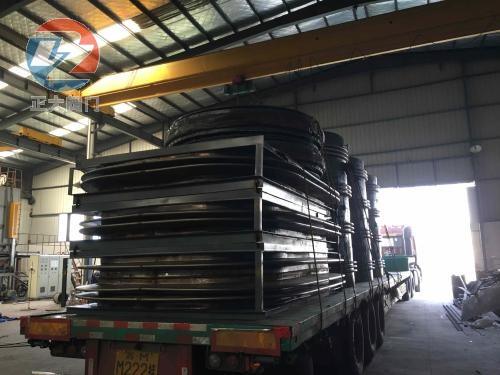